
The Impact of AI on Robotics and Automation
Artificial intelligence is fundamentally transforming robotics, making robots more intelligent, flexible, and capable of performing tasks that were previously impossible or too dangerous for humans. AI-powered robots can learn from their environment, adapt to new situations, and improve their performance over time through machine learning algorithms. This leads to more autonomous manufacturing lines, where robots can handle complex assembly, inspection, and packaging with minimal human oversight.
Automation, driven by AI, is also streamlining processes across industries. Smart automation systems can analyze vast amounts of data in real-time, optimize workflows, and reduce waste. For example, in logistics, AI-enabled automated guided vehicles (AGVs) and drones are revolutionizing warehousing and delivery systems, making them faster and more reliable.
Industrial Applications and Smart Manufacturing
In industrial settings, AI combined with mechatronics is paving the way for Industry 4.0 — the next generation of manufacturing. Smart factories leverage AI for predictive maintenance, quality control, and supply chain optimization. Sensors embedded in machinery collect data, which AI algorithms analyze to predict failures before they happen, preventing costly downtime.
Additionally, AI-driven robotics enhance precision and consistency in production, reducing defects and improving product quality. These advancements lead to more flexible manufacturing systems capable of quickly adjusting to changing demands and customizations.
Ethical and Societal Considerations
As AI-powered machines become more prevalent, ethical and societal considerations also emerge. Issues such as job displacement, data privacy, and safety are central to discussions about AI in mechatronics. It is crucial to develop regulations and guidelines that ensure responsible AI deployment, prioritizing human safety and equitable economic growth.
Moreover, transparency in AI decision-making processes and ensuring machines operate ethically are vital to fostering public trust. Balancing technological innovation with social responsibility will be key to harnessing the full potential of AI and mechatronics for a sustainable and inclusive future.
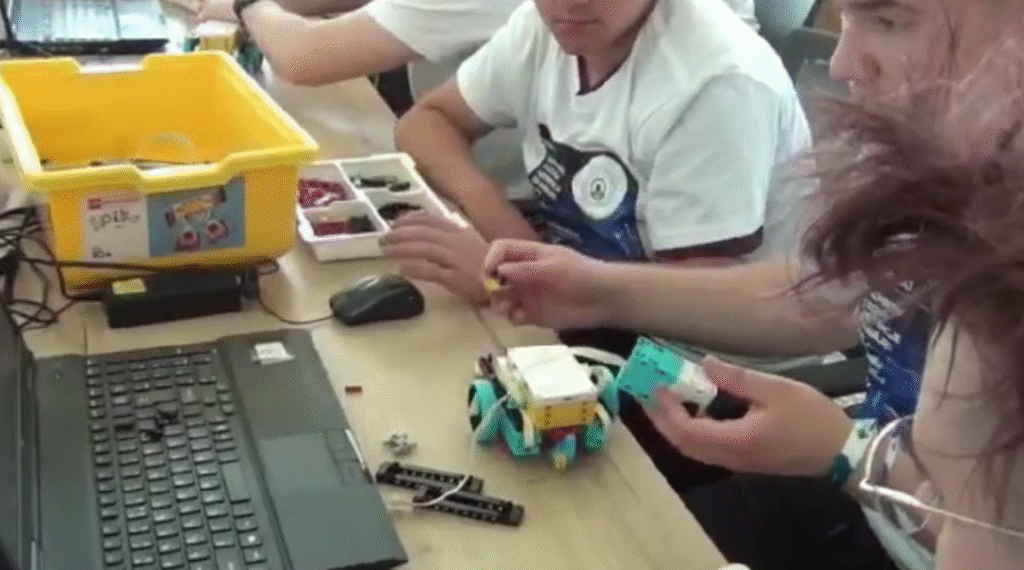

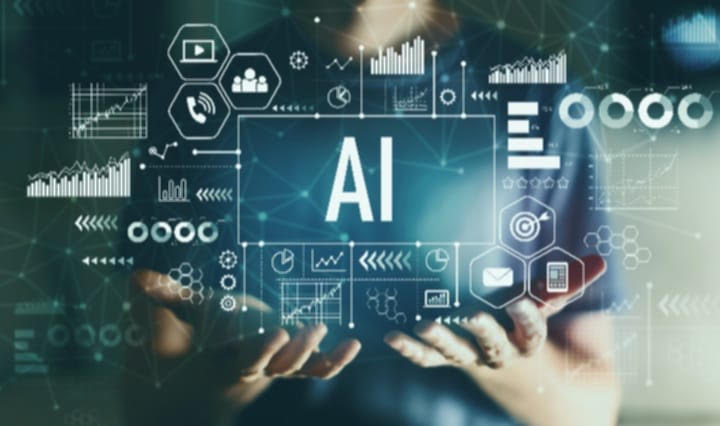
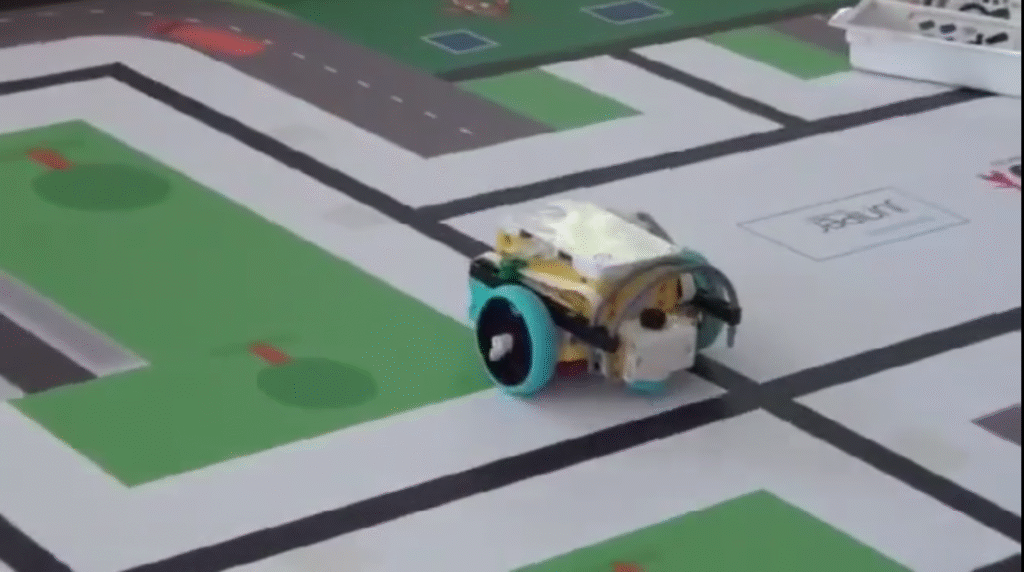
Collaborative Robots in the Workplace
The integration of cobots into industrial and service environments marks a significant shift toward smarter, more adaptable manufacturing and operational processes. Unlike traditional industrial robots, which often operate in isolated cells for safety reasons, cobots are designed to work side by side with humans, sharing tasks and collaborating seamlessly. This transition is driven by advances in artificial intelligence (AI), which empower cobots with perception, decision-making, and communication capabilities.
Enhanced Flexibility and Customization
AI-powered cobots can quickly adapt to changing production requirements, making them ideal for small-batch manufacturing, customization, and complex assembly tasks. Their ability to learn from demonstrations and previous tasks reduces setup times and allows for rapid reprogramming, minimizing downtime and increasing overall responsiveness to market demands.
Improved Safety and Human-Robot Interaction
Safety is paramount when humans and robots share a workspace. AI enables cobots to continuously monitor their surroundings using sensors, cameras, and machine learning algorithms. They can detect human presence, predict human movements, and adjust their actions to prevent accidents. This real-time perception ensures a safe working environment, encouraging more collaborative and less siloed workflows.
Adaptive Learning in Robotics
Artificial Intelligence empowers collaborative robots (cobots) to continuously learn from their environment and user interactions using advanced machine learning algorithms such as reinforcement learning, supervised learning, and deep learning. These capabilities enable cobots to adapt to new tasks, optimize their behaviors, and respond dynamically to environmental changes. Consequently, cobots are becoming increasingly versatile, applicable across a wide array of industries—manufacturing, healthcare, logistics, and more—by customizing their actions, enhancing flexibility, and elevating operational efficiency.
Core Machine Learning Techniques
Reinforcement Learning (RL)
- Principle: In RL, cobots learn optimal actions through trial-and-error interactions with their environment. They receive feedback in the form of rewards for desirable behaviors and penalties for undesired ones.
- Application: For instance, a cobot in a manufacturing setting might learn to navigate a cluttered workspace efficiently or sequence assembly tasks optimally without explicit programming for each scenario.
- Advantages: Enables development of complex, autonomous behaviors such as obstacle avoidance, dynamic task sequencing, and adaptive decision-making.
Supervised Learning
- Principle: Cobots are trained on labeled datasets, allowing them to recognize patterns and make predictions based on prior examples.
- Application: In healthcare, a cobot might learn to interpret medical images, detect anomalies, or recognize patient behaviors, continually improving diagnostic support.
- Advantages: Facilitates precise pattern recognition and classification tasks, essential for tasks requiring high accuracy.
Deep Learning
- Principle: Utilizes neural networks with multiple layers to interpret complex sensory data (visual, auditory, tactile).
- Application: For example, in quality inspection, a cobot can analyze images to identify defects or recognize objects in cluttered environments.
- Advantages: Essential for perception-heavy tasks requiring nuanced interpretation, such as object recognition, scene understanding, or speech processing.
Dynamic Adaptation and Operational Flexibility
Adaptive learning methods allow cobots to handle new or evolving tasks seamlessly, reducing the need for extensive reprogramming:
- Manufacturing: Cobots can observe human workers assembling new product variants, then replicate the process or adapt their actions accordingly.
- Healthcare: Robots personalize care by learning from patient interactions, adjusting treatment approaches, or recognizing individual needs.
- Logistics: Cobots dynamically optimize routes, handling procedures, and inventory management based on real-time data, improving throughput and responsiveness.
This flexibility results in more resilient systems that can operate effectively in unpredictable or changing environments.
Benefits Across Industries
Manufacturing
- Increased resilience: Cobots respond to supply chain disruptions, equipment wear, or product redesigns.
- Minimized downtime: Adaptation allows continuous operation with minimal human intervention for reconfiguration.
Healthcare
- Personalized care: Robots adapt to individual patient needs, anatomical differences, and changing health conditions.
- Enhanced diagnostics: Learning from medical data improves accuracy and efficiency over time.
Logistics and Warehousing
- Navigation & handling: Cobots learn to navigate complex warehouse layouts and manage inventory dynamically.
- Collaboration: They work alongside human workers more efficiently, understanding tasks and safety protocols through ongoing learning.

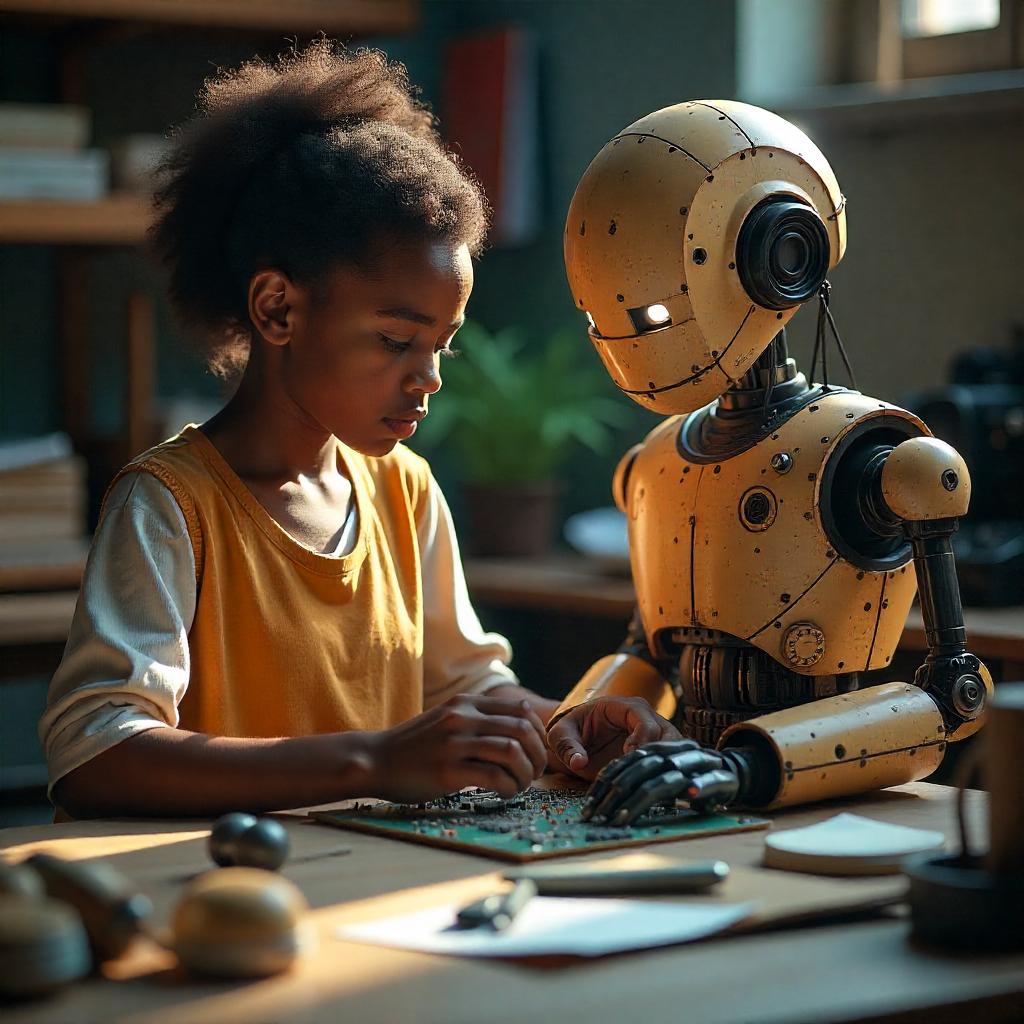
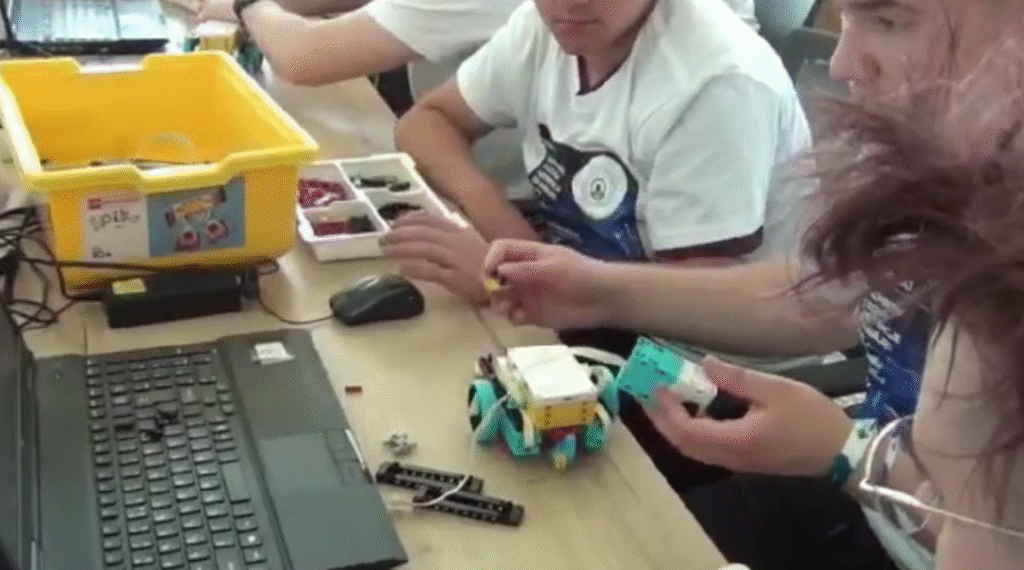
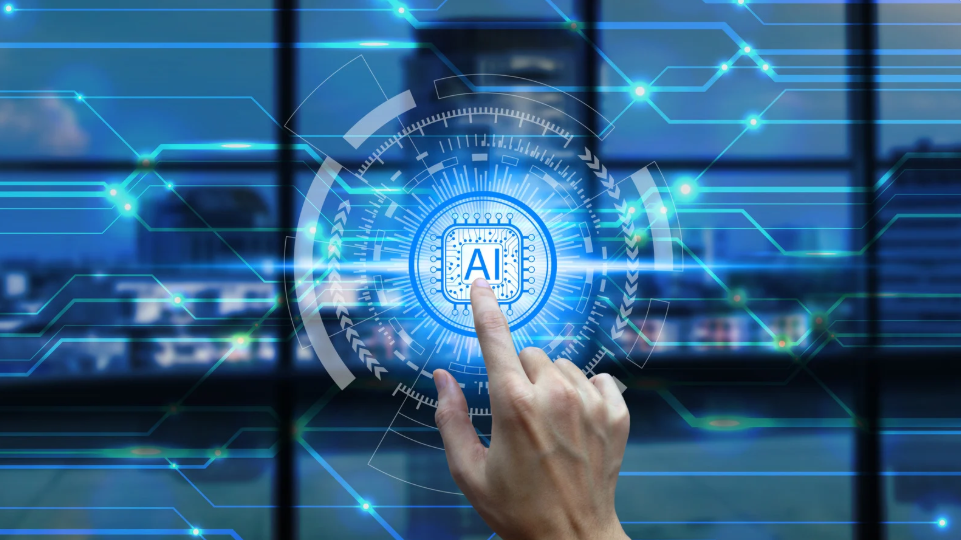
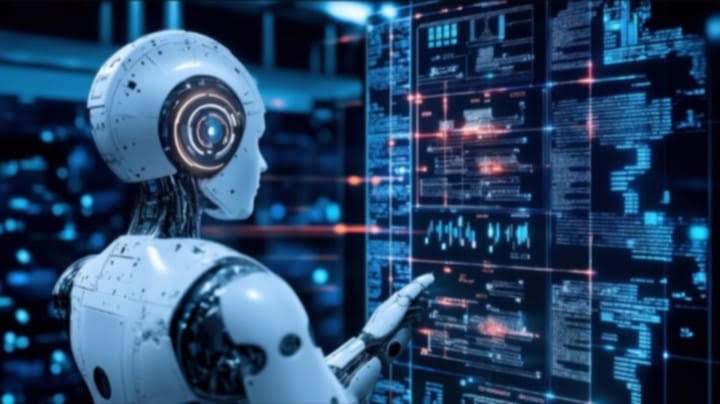
Predictive Maintenance Strategies
AI drives predictive maintenance by analyzing data from sensors, IoT devices, and operational logs using machine learning models like anomaly detection and time-series analysis. These technologies identify patterns indicating potential failures before occurrence. By predicting issues early, AI reduces downtime, lowers maintenance costs, and enhances operational efficiency. This proactive approach ensures system reliability and optimizes resource allocation across mechatronic systems.
Case Studies of Predictive Maintenance Innovation
Case studies include Siemens, which used AI for turbine maintenance, reducing downtime by 30% and maintenance costs by 20%. GE’s AI-enabled rotor monitoring improved failure prediction accuracy, saving millions. Challenges faced involved integrating legacy systems, data quality issues, and staff training. Successful AI deployment led to increased system reliability, cost savings, and minimized unplanned outages, showcasing AI’s transformative impact on mechatronic maintenance.
Broader Insights and Lessons Learned
- Data Quality and Integration: Successful predictive maintenance hinges on high-quality, comprehensive datasets. Legacy systems often lack the necessary instrumentation, necessitating upgrades or middleware solutions.
- Organizational Change: Transitioning to AI-driven maintenance requires cultural shifts, emphasizing data literacy, trust in automation, and cross-disciplinary collaboration.
- Scalability and Customization: Tailoring AI models to specific equipment and operational contexts enhances prediction accuracy but demands ongoing tuning and validation.
Impact and Future Trends
These case studies highlight how AI-powered predictive maintenance can lead to:
- Reduced operational costs
- Enhanced equipment lifespan
- Increased safety and reliability
- Minimized unplanned outages
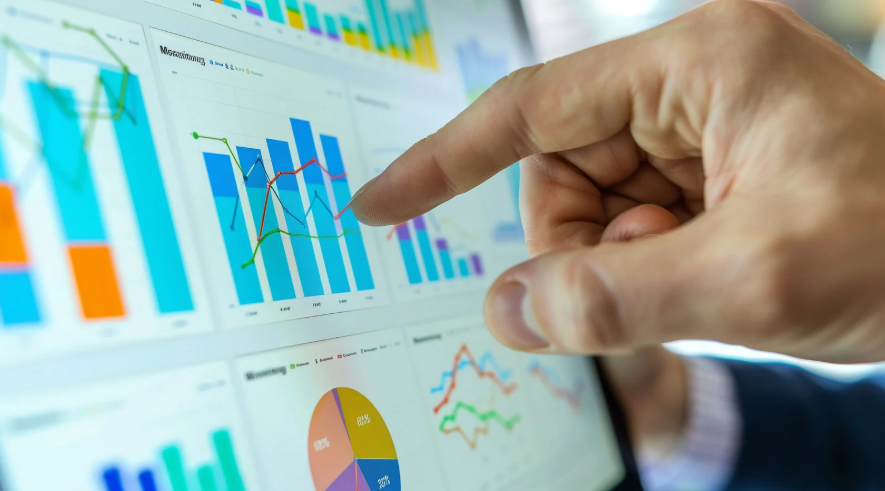
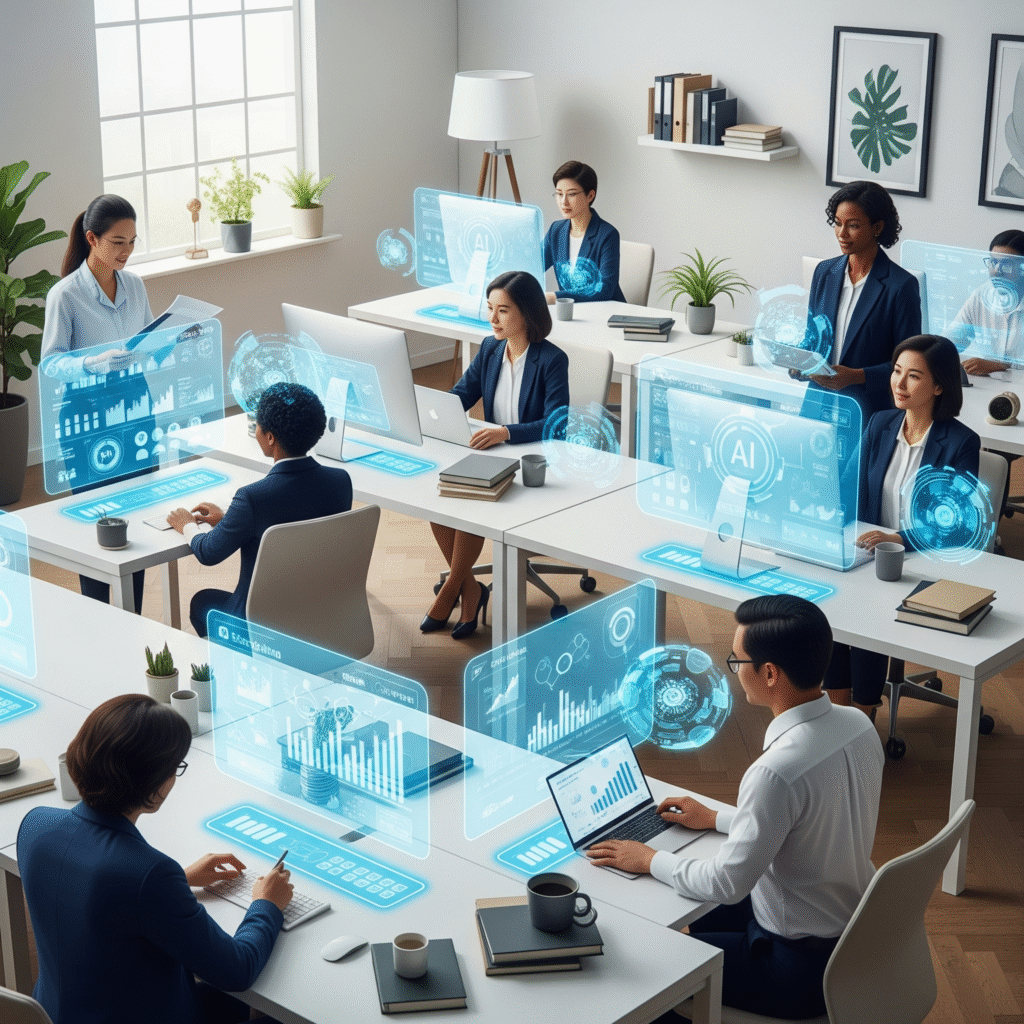
Real-Time Data Analysis for Operational Insights
Real-time data analysis is vital in mechatronics for immediate detection of anomalies, optimizing performance, and preventing failures. AI algorithms process vast sensor data through techniques like deep learning and streaming analytics, identifying patterns and anomalies instantly. This enables dynamic adjustments, predictive insights, and informed decision-making, leading to improved efficiency, reduced downtime, and enhanced system reliability in complex mechatronic environments.
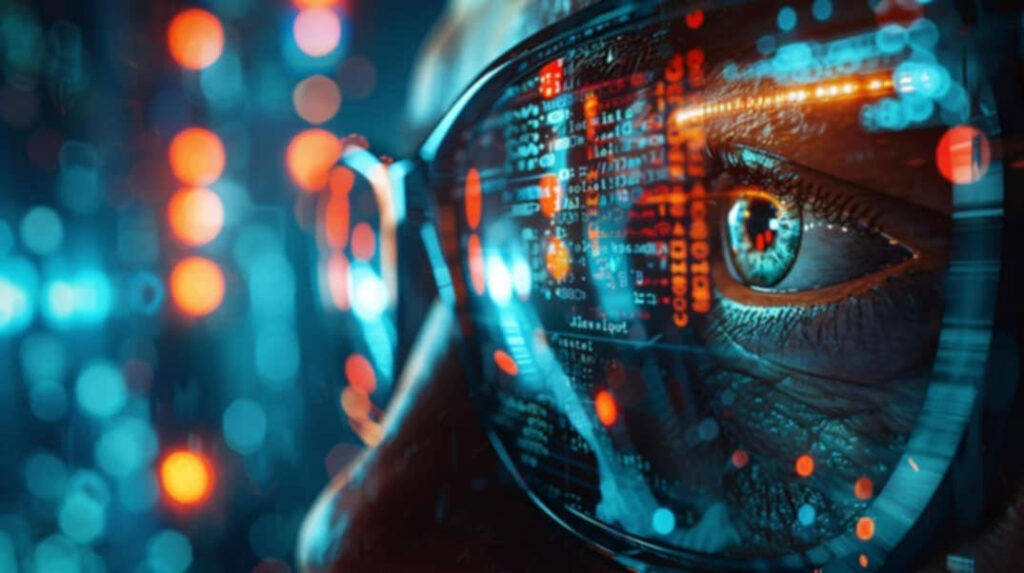
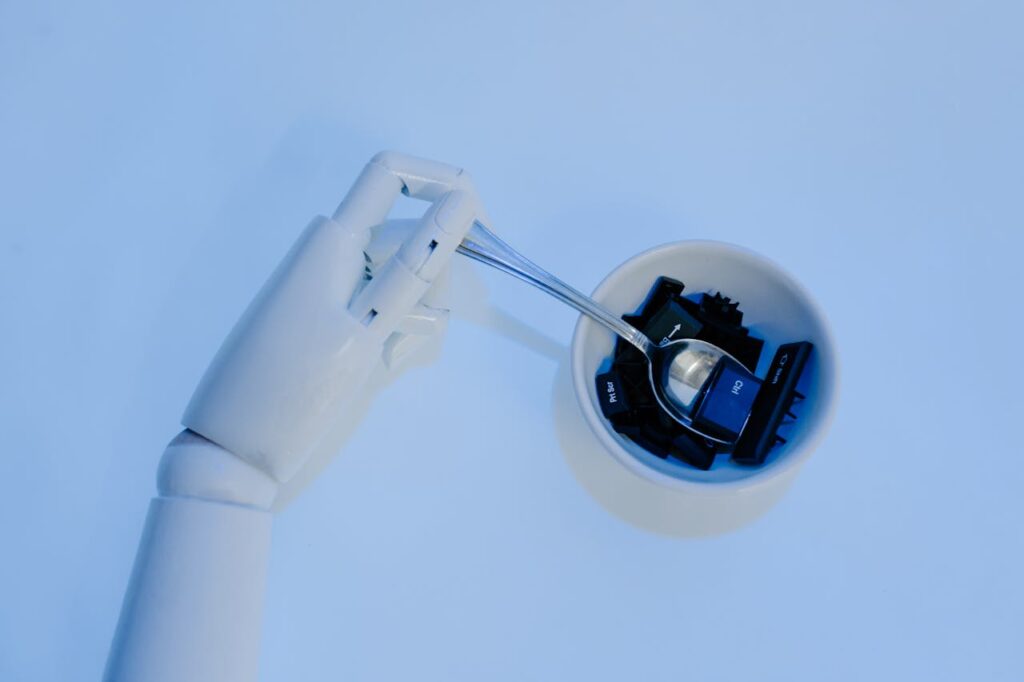
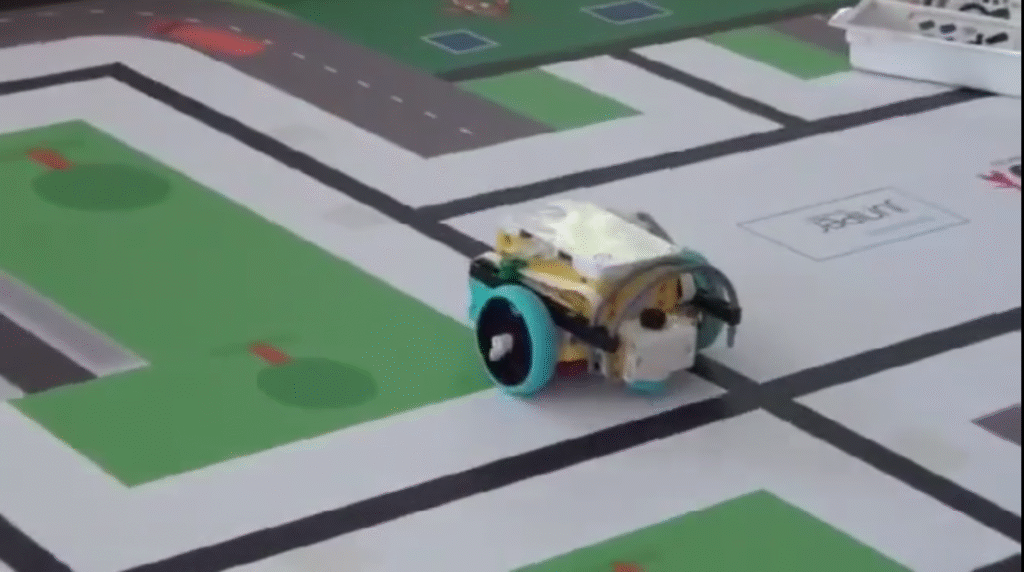
Integrating IoT with AI and Mechatronics
The integration of Internet of Things (IoT), Artificial Intelligence (AI), and mechatronics represents a transformative approach to building intelligent, autonomous systems. This convergence leverages the strengths of each technology to create interconnected, adaptive machines that can sense, analyze, and act in real-time, revolutionizing industries from manufacturing to robotics.
The Synergy of IoT, AI, and Mechatronics
IoT (Internet of Things): Provides the infrastructure for interconnected devices, sensors, and actuators that collect and transmit vast amounts of data across systems. IoT enables real-time monitoring, remote control, and seamless data flow between machines and cloud platforms.
AI (Artificial Intelligence): Processes and analyzes the data collected via IoT sensors to generate insights, make predictions, and optimize decision-making. AI algorithms, including machine learning and deep learning, empower systems to learn from data, identify patterns, and adapt behaviors autonomously.
Mechatronics: Combines mechanical systems, electronics, control engineering, and software to develop sophisticated, responsive machines. When integrated with IoT and AI, mechatronic systems become smarter, capable of autonomous operation and dynamic adjustments.
AI’s Role in Quality Control
Artificial Intelligence (AI), particularly machine learning (ML), is revolutionizing quality control processes within mechatronics and manufacturing industries. By leveraging advanced data analysis, image recognition, and predictive capabilities, AI enables organizations to perform more accurate, faster, and cost-effective inspections, ultimately ensuring higher product quality and customer satisfaction.
How AI Enhances Quality Control
Automated Defect Detection:
AI-powered image recognition systems can analyze visual data from cameras and sensors during production. These systems identify surface defects, misalignments, or missing components with precision, surpassing traditional manual inspections in speed and accuracy. For example, in electronics manufacturing, AI can detect tiny soldering faults or component misplacements that are difficult for human inspectors.Sensor Data Analysis:
Mechatronic systems are equipped with sensors monitoring parameters such as temperature, vibration, pressure, and dimensions. Machine learning models process this sensor data to detect anomalies indicative of potential defects or process deviations. Early detection allows for immediate corrective actions, reducing scrap rates and rework costs.Process Optimization:
AI models learn from historical production data to optimize manufacturing parameters dynamically. For instance, they can adjust machine settings to prevent defect formation, ensuring consistent quality across batches. This continuous learning capability helps maintain high standards even as materials or environmental conditions change.
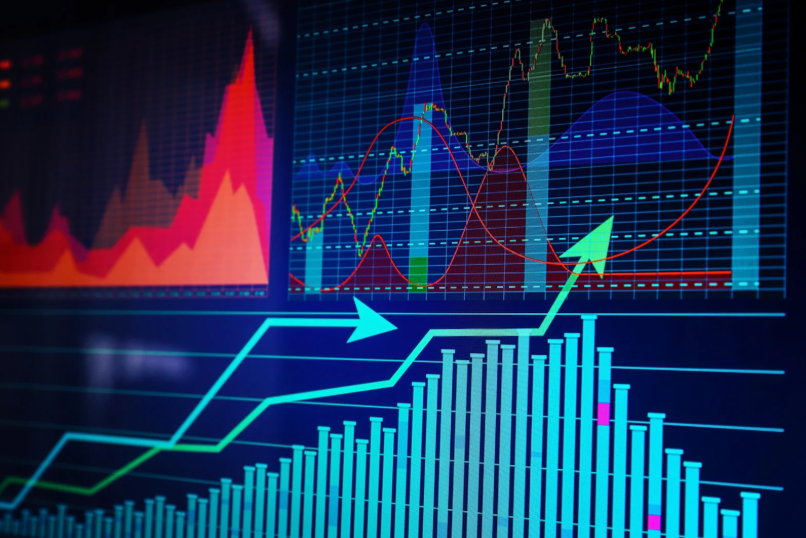
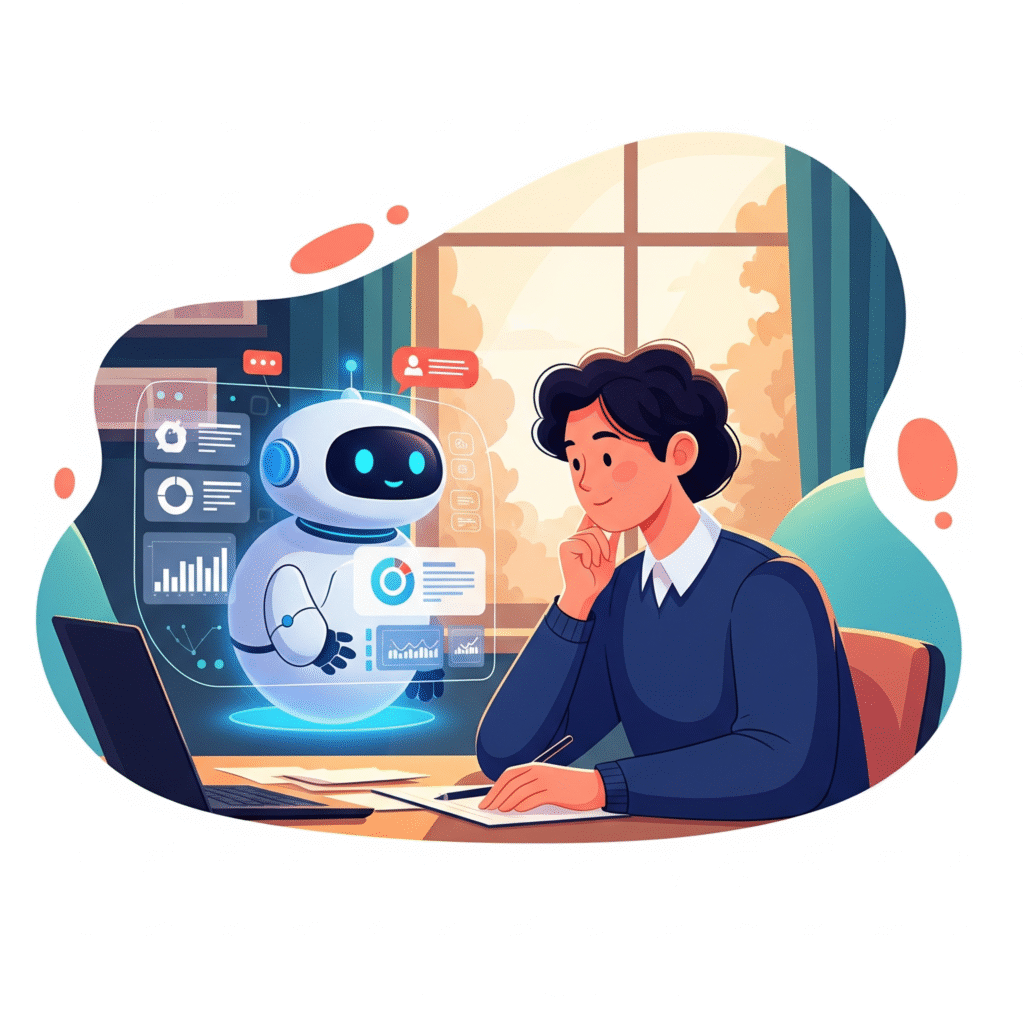
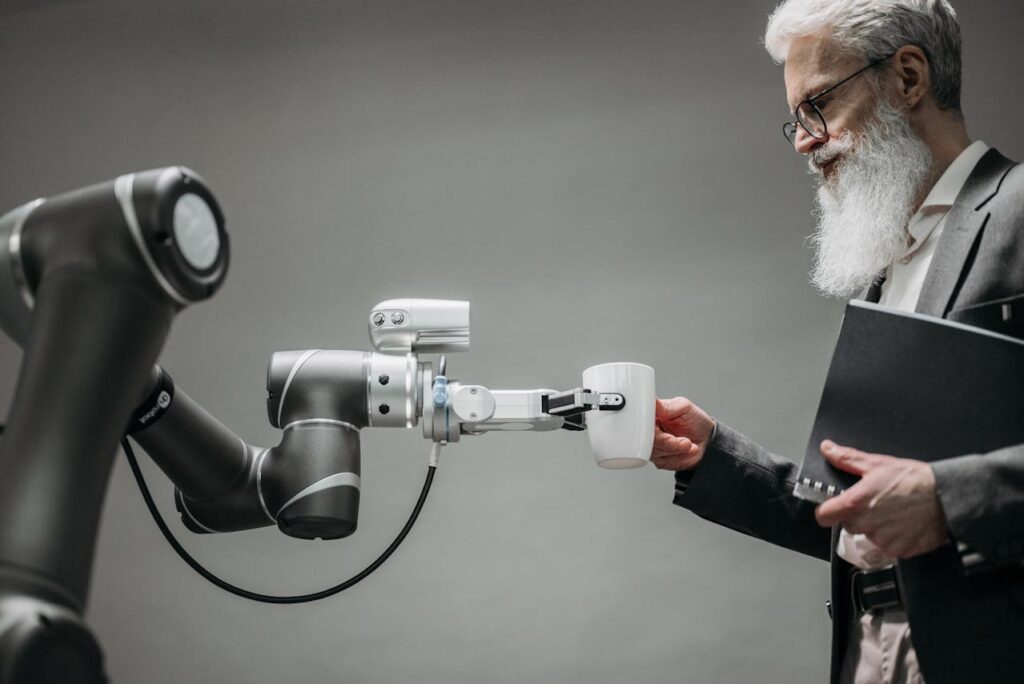
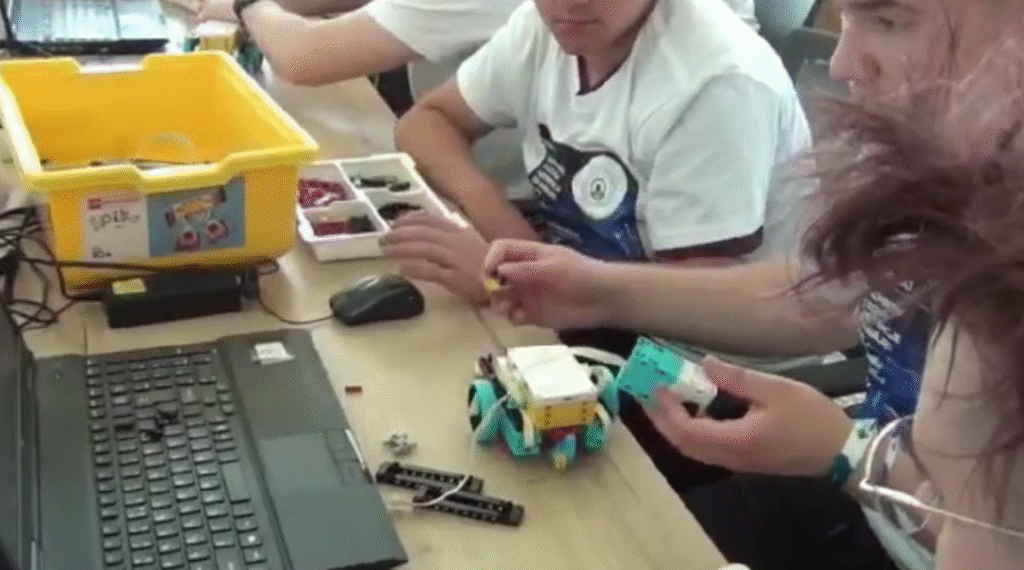
Ethical Considerations in AI-Driven Manufacturing
As AI becomes increasingly integrated into mechatronic systems and manufacturing processes, it raises vital ethical questions that organizations, policymakers, and society must address. Ensuring responsible development and deployment of AI technologies is essential to maximize benefits while mitigating potential negative impacts.
Key Ethical Challenges
Job Displacement and Workforce Impact:
AI-driven automation can lead to significant shifts in employment, with routine and manual jobs replaced by machines. While increased efficiency is beneficial, it raises concerns about unemployment, economic inequality, and social stability. Responsible companies must anticipate these impacts and develop strategies to support affected workers.Autonomous Decision-Making and Accountability:
AI systems capable of making autonomous decisions—such as adjusting manufacturing parameters or even performing quality inspections—pose questions about accountability. Who is responsible if an AI system makes an error that causes defects, safety hazards, or legal violations? Ensuring clear lines of responsibility is a critical ethical consideration.Transparency and Explainability:
Black-box AI models can be opaque, making it difficult for humans to understand how decisions are made. Lack of transparency can erode trust among workers, consumers, and regulators. Promoting explainable AI helps stakeholders comprehend decision processes and fosters accountability.Bias and Fairness:
AI models trained on biased data may produce unfair or discriminatory outcomes, affecting worker safety, customer treatment, or product quality. Vigilant data management and fairness assessments are necessary to prevent unethical biases.Data Privacy and Security:
AI systems often rely on vast amounts of data, including sensitive information about workers, processes, or products. Protecting this data from breaches and misuse is a moral obligation to respect privacy rights.